Steam Shovel
Sometime in 1894, while his Great Lakes steamer W. P. Thew lay tied to a Cuyahoga River wharf in northeast Ohio, 48-year-old Capt. Richard P. Thew, failed farmer and hardware salesman, observed a railroad steam shovel take one clumsy scoop of ore after another from the heap on the wood docks and dump them into a hopper car sitting on nearby railroad tracks. He noticed that the shovel bucket’s teeth gouged the dock’s timbers and left much of the ore behind.
Built for heavy-duty earthmoving of canals or digging of railroad cuts, the steam shovels of 1894 were poor tools for scooping from level ground. Each had a dipper stick that bobbed up and down on a pivot point midway down a diagonal crane boom, a setup that limited motion to heavy-handed arcs.
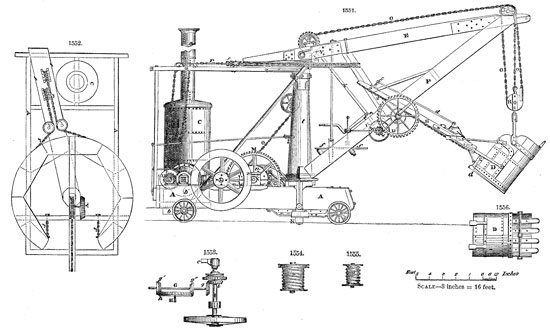
Remarkably, no one had addressed this particular problem since Philadelphia civil engineer William Otis had patented his first “Steam Excavator” shovel in 1839. Its first major job was digging the Welland Canal in 1843, when dozens of displaced laborers grew so angry that the company had to post guards on the site. For decades afterward, Otis’s successors stifled innovation by declining to freely license production in the United States. In addition, American industry refused to adapt its big iron to fit other niches. Digging a sewer trench along a city street or loading up clay at a brick factory, for example, were no jobs for a 70-ton railroad shovel.
Thew wondered whether he could tame Otis’s ungainly shovel design by mounting the dipper with a sliding pivot, which would more closely mimic the agility of the human arm. And by focusing on just one of the industry’s unopened niches, the handling of iron ore at fragile docks, Thew helped it onto a new track and converted himself from a hardscrabble boat captain to a landlubbing millionaire.
In 1895 he enlisted shovel expert Holley Harris to transform his ideas into blueprints, then hired a Cleveland job shop named Variety Iron Works to build a working prototype. It attracted the attention of Marcus A. Hanna, an iron magnate and Republican kingpin, who bought the first one to run his Cleveland Pittsburgh Ore Dock. Thew gave up his boat job to meet the ever-mounting demand, and in 1899 he joined with businessmen in Lorain, Ohio, to open a factory.
The success of what catcallers dubbed “Thew’s merry-go-round” came as a rude surprise to loyal users of Bucyrus, Marion, Vulcan, and other such sturdy machines, particularly because the newcomer had been designed by a man without heavy construction or mining experience. The disparaging term referred to the shovel’s most visibly striking feature, its turntable, which looked like more trouble than it was worth—to the manufacturers, at any rate. While British maker Whitaker & Sons had offered the first steam shovel with a full-swing capability 10 years earlier, no American steam shovel could swing in much more than a half-circle, because they were all mounted at the ends of flatcars. The ability to turn sped up work greatly. Such a shovel could load cars in all directions, carry its own counterweight to balance much more effectively at full reach, and dig its way out of a landslide that would trap a railroad shovel. In time every operator would insist on it.
There was more: Thew’s compact machine needed no rails; with solid ground or planking underfoot, it operated on steel wheels driven by the shovel’s steam engine, the operator steering by swinging the turntable from side to side. (Caterpillar tracks would come later.) Wire rope did the heavy lifting, a distinct advance over the former standard chain-lift because steel cables ran more safely and smoothly over the sheaves. Thew’s attention to simpler controls reduced the crew size from three men to two.
In a unique feature that directly addressed the ore-handling market, Thew installed a “horizontal-crowd feature” that carried the pivot for the dipper stick, deployed by the operator along a horizontal track mounted on the boom. This allowed the bucket to slide forward five feet and take a level bite before the lift-cable swung it upward.
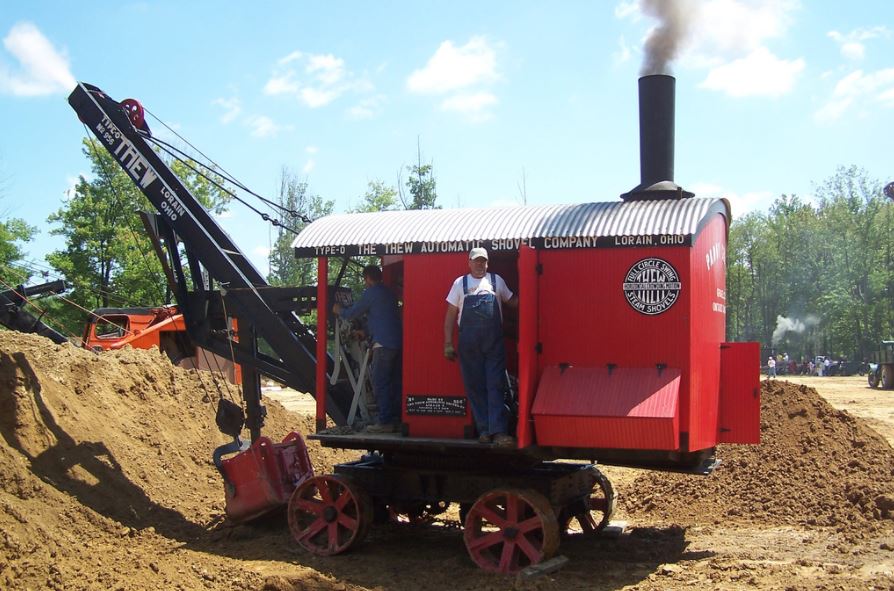
Thew continued to expand his market. Because nobody else was offering such a small and nimble machine, he sold shovels to Klondike gold miners, builders of western irrigation ditches, and street contractors whose operators found the leverage offered by the horizontal-crowd mechanism ideal for prying up old slabs of concrete. One Thew shovel helped dig a lock through the mountains for the Panama Canal.
In time the greater dexterity of a new class of back-dragging shovels—driven by internal combustion engines and actuated by hydraulic fluid—would push all steam shovels out of the catalogs, but Thew adapted. In 1914 his company was one of the first in America to introduce the gasoline-powered shovel that dominates the modern market. But the end of production isn’t the same as extinction. Hundreds of Thew shovels worked mines and road cuts into the 1950s, and today a few can still work up a head of steam.